Understanding PLCs: Function, Architecture, and Impact
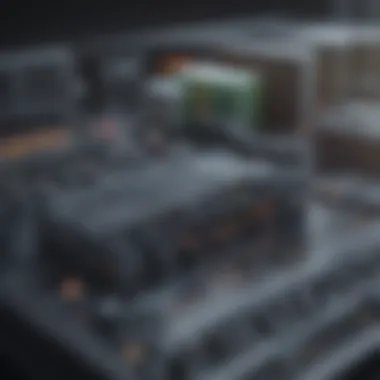
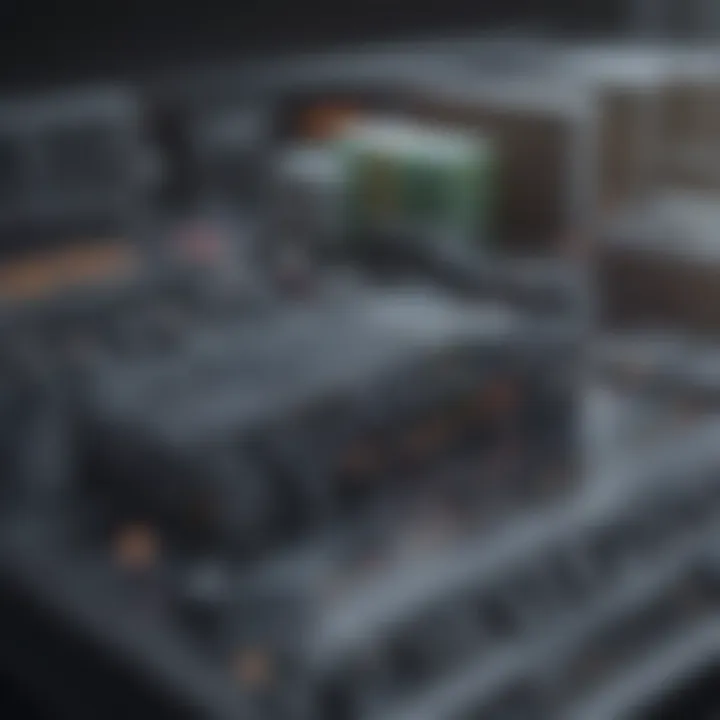
Intro
Programmable Logic Controllers, or PLCs, have become a cornerstone in the realm of industrial automation. They operate behind the scenes, controlling machinery and processes in factories, buildings, and various systems. PLCs streamline operations, enhance efficiency, and ultimately help businesses save time and money. Understanding PLCs is not only crucial for industry professionals but also for investors who are keen to grasp technological advancements that drive modern industry forward.
As we navigate through this article, we will dissect what makes PLCs tick. Weโll cover their fundamental architecture, historical development, and notable applications across industries. By the end of this exploration, readers will have a nuanced understanding of PLCs, which will aid in any decision-making related to investing in automation-related technologies.
Investment Terminology Breakdown
Key Terms Explained
In the context of PLCs and their significance in investment, familiarizing oneself with specific terminology is pivotal. Here are a few key terms:
- Automation: The use of technology to perform tasks with minimal human intervention, which is where PLCs shine.
- Real-time Processing: Refers to the ability of PLCs to react instantly to input signals to drive outputs, fundamental in time-sensitive manufacturing processes.
- Scalability: A crucial aspect of PLCs, indicating how easily systems can be expanded or modified as business needs grow.
- Data Logging: PLCs often come equipped with data logging capabilities, allowing for monitoring and analysis of operational data over time.
Understanding these terms equips investors and professionals with the lexicon needed to communicate effectively about PLC systems and their broader implications in industry.
Common Misconceptions in Investing
A few myths around PLC investment abound that can mislead potential investors:
- PLCs are only for big industries: Many believe that PLCs are reserved solely for large factories, whereas small and medium enterprises increasingly leverage PLCs for automation, presenting investment opportunities.
- Implementation is too complex: While integrating PLCs requires expertise, innovations in user-friendly software have simplified installation and operation, lowering the barrier to entry.
- They are outdated technology: Some view PLCs as relics of past technology. However, they continue to evolve, with cloud capabilities and IoT integration enhancing their value.
By dispelling these misconceptions, investors can better position themselves within the growing landscape of PLC technology.
Financial Product Reviews
In-Depth Product Analysis
When looking into PLC-related financial products, several offerings stand out. Investors must evaluate PLC manufacturers, software solutions, and integrated systems. Notable companies in this space include Mitsubishi Electric, Siemens, and Allen-Bradley. Each provides a variety of solutions tailored to different sectors, from food production to oil refining.
- Mitsubishi Electric: Known for their versatile PLC systems, suitable for fast-paced environments, integrating robust data logging and user-friendly interfaces.
- Siemens: Offers a wide range of automation products, backed by solid support networks and a reputation for innovation in engineering.
- Allen-Bradley: Their PLCs are well-regarded for reliability and ease of integration into existing industrial ecosystems.
Pros and Cons of Each Offering
Mitsubishi Electric
- Pros: Highly customizable; often provides excellent support.
- Cons: Can be pricier than some competitors.
Siemens
- Pros: Robust engineering reputation; extensive ecosystem of products.
- Cons: Complexity in integration can be a hurdle for smaller businesses.
Allen-Bradley
- Pros: Known for reliability; easy integration with existing setups.
- Cons: Support mainly available in specific regions.
"The choice of a PLC system can define operational efficiency for industries, thus having profound implications on investment decisions as well."
As we progress through this article, remember that understanding PLCs is key not only to recognizing their immediate applications but also for making sound investment choices in a tech-driven future.
Understanding Programmable Logic Controllers
The significance of understanding Programmable Logic Controllers (PLCs) cannot be overstated, especially in a landscape where automation is becoming the backbone of numerous industries. The effectiveness of modern industrial processes hinges on the reliability and functionality of these devices. PLCs transform how machinery operates, enabling complex processes to be controlled with precision. Investors and professionals alike should view PLCs not just as hardware, but as the linchpin that connects advanced technology to operational efficiency.
At their core, PLCs are specialized digital computers designed for industrial automation. They accept various inputsโbe it from sensors, switches, or other devicesโand, based on programmed logic, produce outputs to control machinery, processes, or systems. This capability makes them invaluable across sectors such as manufacturing, transportation, and building management. The importance of this understanding lies in recognizing the potential cost savings, productivity boosts, and safety enhancements that PLCs can deliver.
Consider the following key elements:
- Adaptability: PLCs are designed to be flexible, allowing them to be programmed and reprogrammed to meet evolving operational needs.
- Robustness: Built to endure harsh industrial environments, PLCs can operate under varied conditions, ensuring reliability in critical operations.
- Integration: Modern PLCs can integrate with other technologies, such as IoT devices, facilitating smarter operations through data exchange and streamlined processes.
In essence, grasping the workings of PLCs equips investors and professionals with the insights needed to evaluate potential investments and innovations in automation technology. This understanding is a crucial cornerstone for anyone looking to engage with the future of industries impacted by automation.
The Core Functionality of PLCs
Understanding how PLCs function is fundamental to leveraging their capabilities in industrial settings. These devices process input signals from various sensors or user interfaces, execute a programmed set of instructions, and deliver output signals to control different elements of machinery or processes.
The operation typically follows a cycle, often described as Input-Process-Output:
- Input: Signals are received from devices such as switches, sensors, or other inputs, informing the PLC about the current state of the system.
- Process: Based on predefined programming, usually done in ladder logic or structured text, the PLC analyzes the inputs and makes decisions.
- Output: The outcomes of these decisions trigger actions such as starting a motor, opening a valve, or sending alerts to operators.
This cycle happens repeatedly and rapidly, allowing for real-time control over processes. Moreover, PLCs can be programmed to handle operational contingencies, enhancing both efficiency and safety.
Historical Context and Evolution
To fully appreciate PLC technology, it's essential to consider its historical background. Initially developed in the late 1960s as a solution to replace hardwired relay systems, PLCs introduced a new era in industrial automation. The first commercially available PLC was introduced by Modicon in 1968, aimed at simplifying the control of manufacturing processes.
Over the decades, PLCs evolved dramatically:
- 1970s: Introduction of modular systems, allowing for more complex control systems tailored to specific industries.
- 1980s and 1990s: The rise of networking capabilities, enabling PLCs to communicate with computers and other machines.
- 2000s and beyond: Integration of advanced technologies like IoT, enhancing their functionality and paving the way for smart factories.
This historical perspective sheds light on the technological advances that have shaped current PLC capabilities. For investors, understanding these developments can provide insights into the market dynamics of the automation industry, signaling growth opportunities and areas ripe for innovation.
"The evolution of PLC technology illustrates the relentless pursuit of efficiency and adaptability in industrial settings."
In reflection, the depth of knowledge about PLCs creates a solid foundation for further exploration into their components, types, applications, and the future of this technology. As industries delve deeper into automation, those familiar with PLCs will likely find themselves at a pivotal crossroads of opportunity.
Key Components of PLC Systems
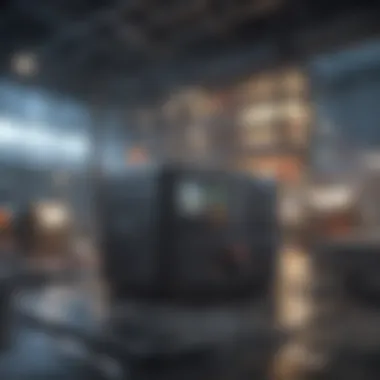
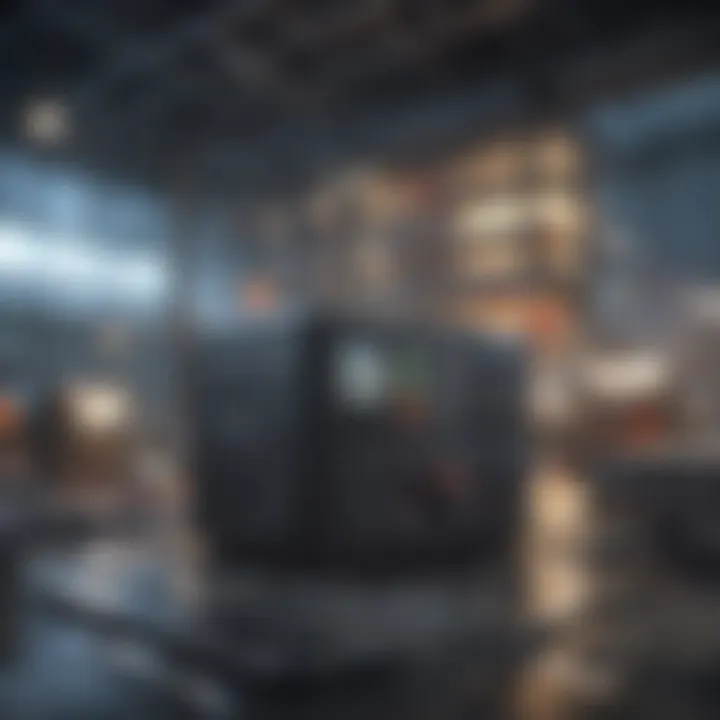
Understanding the key components of PLC systems is integral to grasping how these devices function within the realm of automation. Each element plays a crucial role that contributes to the overall efficacy, reliability, and adaptability of Programmable Logic Controllers. In this section, we shall discuss the individual components which together form the backbone of PLC technology and elaborate on their significance in ensuring smooth operations in various industrial settings.
Central Processing Unit (CPU)
The Central Processing Unit (CPU) can be likened to the brain of a PLC system, overseeing all operations and making instantaneous decisions based on programmed instructions. A CPU executes the control logic needed to process input signals, manage commands, and generate output responses. A certain type of CPU might be better suited for specific applications, whether it is for simple tasks or complex processes requiring high-speed execution.
- Features of the CPU include:
- Real-time processing capabilities
- Multi-tasking operations
- Ability to handle diverse data types
Understanding the CPUโs role assists investors in evaluating which PLC systems are likely to provide competitive advantages. The efficiency and power of the CPU directly impact the PLCs' performance, ultimately influencing operational costs and production outputs.
Input and Output Modules
The Input and Output Modules act as the sensory and motor organs of the PLC. Input modules are responsible for receiving and interpreting signals from connected devices, such as sensors and switches. Conversely, output modules send commands to actuators and other machines, influencing their behavior according to the logic defined in the CPU.
- Important points about these modules:
- Input modules can handle digital or analog signals.
- Output modules define how precise and timely commands are relayed to machinery.
- They are often where failures occur, hence maintenance and quality are paramount.
The effectiveness of the input and output modules directly affects the accuracy of the production process, making it a significant consideration for PLC users and investors alike.
Power Supply Units
The Power Supply Unit (PSU) ensures the entire PLC system is energized. Just as a vehicle requires fuel to run, a PLC needs a stable and reliable power supply to maintain its operations without interruptions. The PSU converts electrical power to levels suitable for the CPU and other components, supporting consistent communication and processing.
- Key aspects of power supply units include:
- Voltage stability and safety features.
- Protection against electrical fluctuations, which could lead to catastrophic failures.
- Energy efficiency, keeping running costs low.
Investors should look for PLCs with robust PSU designs since power reliability can be a make-or-break factor in maximizing uptime and reducing operational expenses.
Programming Devices
Last but not least, the Programming Devices are essential for initial configuration and ongoing adjustments of the PLCโs programmed logic. They typically come in various forms, ranging from handheld programmers to advanced software integrated into more complex systems.
- Considerations regarding programming devices:
- User-friendly interfaces increase accessibility for operators.
- Compatibility with different programming languages can widen the application spectrum.
- Availability of remote programming options, facilitating easy updates and modifications.
The choice of programming device can impact how swiftly and effectively changes can be implemented in real-time, contributing to more agile operations. For investors, understanding the nuances of how programming impacts a PLCโs adaptability can pave the way for strategic investment decisions.
In summary, the core components of PLC systemsโCPU, input and output modules, power supply units, and programming devicesโconstitute the essential framework that operates myriad automation tasks. Recognizing their significance enables stakeholders to make well-informed decisions when considering investments in PLC technologies.
Types of PLCs
When delving into the realm of Programmable Logic Controllers, it is fundamental to understand the various types of PLCs available. Different types cater to distinct operational needs, making them suitable for a variety of applications across industries. Selecting the appropriate type is crucial as it directly affects system performance, expandability, and integration into the broader automation framework. By discerning the nuances among these types, investors and professionals can make informed decisions that align with strategic goals and operational efficiency.
Standard PLCs
Standard PLCs are the workhorses of automation systems. They come equipped with essential features that cater to most industrial applications. Their architecture typically includes a CPU, input and output modules, and a power supply integrated within a single unit. These PLCs are highly reliable and generally designed to manage a moderate number of inputs and outputs.
What truly sets standard PLCs apart is their robustness. They are built to perform under rugged industrial conditions, making them ideal for manufacturing environments. Moreover, their ease of programming using Ladder Logic is a significant advantage, particularly for facilities where operators are already familiar with this methodology.
Compact PLCs
Compact PLCs are an excellent choice for applications where space is at a premium. Unlike standard PLCs, these devices combine the CPU, I/O, and power supply into a compact unit. This makes them exceptionally versatile and widely used in smaller machinery and applications that do not require extensive I/O.
The primary benefit of compact PLCs lies in their simplicity and lower cost. For investors or businesses aiming to optimize expenses while maintaining sufficient automation capabilities, compact PLCs can be an ideal solution. However, it's essential to consider that with this reduction in size, there's also a limit on expandabilityโmeaning they may not be as suitable for larger, more complex systems.
Modular PLCs
When scalability is a priority, modular PLCs can be a game changer. These PLCs feature a design that allows users to add or swap out components such as input and output modules as needed. This flexibility positions modular PLCs as a preferred choice for applications that may evolve over time, such as in manufacturing pipelines where processes change frequently.
The capability to customize the system configuration makes modular PLCs valuable for large systems needing significant input and output handling. For investors, the initial investment might be higher compared to compact models, but the long-term operational benefits can offer a substantial return on investment through adaptability and reduced downtime.
Safety PLCs
In sectors where safety is the top priority, such as chemical processing or heavy machinery operations, safety PLCs play a pivotal role. These controllers are designed to adhere to stringent safety standards and employ redundant systems to ensure fail-safe operations. They monitor system operations constantly and can trigger safety measures if they detect anomalies.
Safety PLCs often incorporate features like emergency stop functions and safety interlocks. For companies deeply invested in workplace safety, these PLCs provide a safeguard against accidents and operational hazards. In a sense, they protect not just the machinery but also the workforce, making them indispensable for industries where safety cannot be compromised.
"The choice of a PLC type can significantly impact both the operational efficiency and safety of the automation system."
In summary, the right type of PLC can greatly enhance productivity and reduce risks in various applications. With considerations around space, flexibility, safety, and cost, investors and professionals must carefully evaluate their options to select the most suitable PLC type for their automation needs.
Programming Languages for PLCs
In the domain of automation, the programming languages used for Programmable Logic Controllers (PLCs) serve as the backbone of control systems. The choice of a programming language can significantly impact the performance, reliability, and adaptability of automation solutions. Given the variety of tasks that PLCs might be assigned, understanding the nuances and applications of different programming languages is vital.
Ladder Logic
Ladder Logic has a storied reputation as one of the most dominant programming languages in the PLC arena. Originally designed to mimic the look of electrical relay logic diagrams, it allows engineers to visualize circuits, making it accessible, especially for those with a background in traditional electrical engineering.
One of its key benefits is ease of understanding. Users can quickly identify the control logic since the format resembles electrical schematics. However, a downside appears when dealing with complex processes. Ladder Logic can become cumbersome, leading to potential oversight or errors. Itโs most effective in simpler applications where the logic is straightforward.
In its use, many industries still rely on it, particularly in manufacturing where the principles were first ingrained. The versatility of Ladder Logic makes it particularly appealing in sectors where legacy systems are prevalent, allowing for seamless integration.
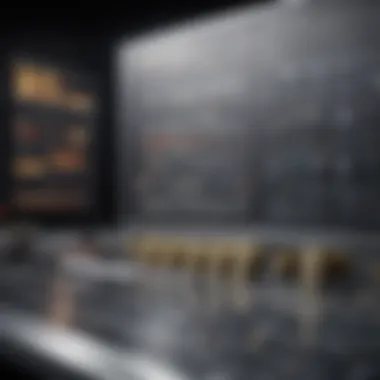
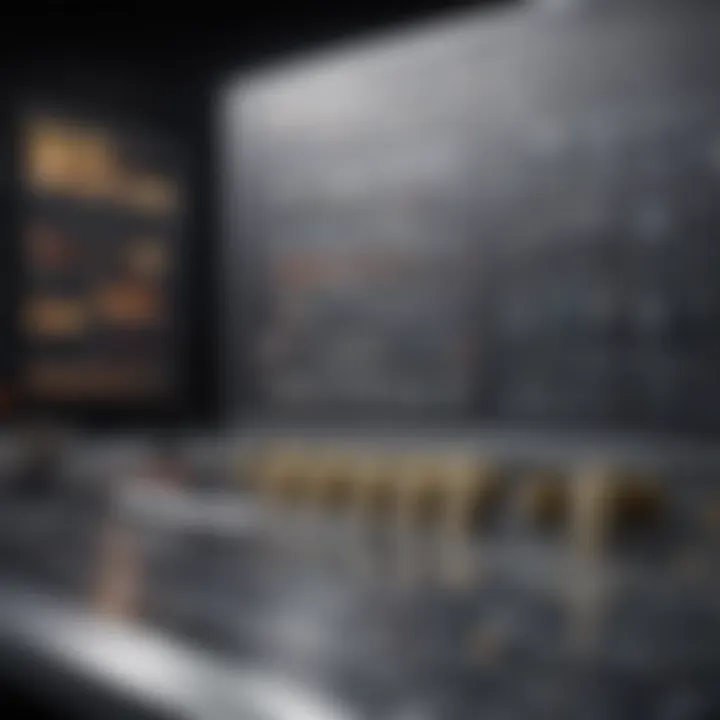
Structured Text
Structured Text introduces a different facet of PLC programming, operating almost like a modern programming language. This high-level language opts for a textual format, where instructions are written in a syntax that resembles Pascal or C.
Investors looking to delve into this mode should recognize its efficacy in handling complex algorithms. With the rising need for intricate control systems, Structured Text stands out for its ability to tackle complex data operations and intricate calculations with relative ease. However, there is a learning curve. For the uninitiated, it may feel more daunting compared to Ladder Logic.
Furthermore, its capability to support programming constructsโsuch as loops and conditionalsโmeans structured programming avidly improves clarity and manageability over time.
Function Block Diagram
Function Block Diagram (FBD) exhibits a graphical approach similar to Ladder Logic but focuses more on the functional relationships between inputs and outputs. Each block represents specific functionsโthink of it like visualizing a flowchart for the logic of control processes.
This visual representation enables a broad understanding of how various elements interact, making troubleshooting significantly easier. For industries that emphasize process control, like water treatment or chemical processing, Function Block Diagrams offer a brilliant means to manage intricate systems without drowning in complexity.
Its primary drawback could be that it becomes difficult to scale for exceedingly complicated processes; nevertheless, it shines in modular applications where blocks can be reused, making it efficient design-wise.
Instruction List
Instruction List (IL) is perhaps the least commonly used but remains important. This low-level language operates similarly to assembly languages and provides a concise way to program PLCs. The straight-to-the-point style of IL can produce compact programs, making it an appealing option for resource-strapped environments.
However, the major issue with IL is the clarity. It can be a struggle to maintain readability, especially as the code grows. As a result, it's more suited for applications with strict size constraints or when rapid performance is vital.
"Selecting the right programming language for PLCs can mean the difference between straightforward functionality and a tangled mess of wiresโfiguratively speaking."
In summary, different programming languages for PLCs bring unique benefits and challenges. Understanding these languagesโLadder Logic for its traditional grasp, Structured Text for complexity, Function Block Diagrams for clarity, and Instruction List for brevityโcould foster sharper decision-making in automation investments. Investors are advised to take a comprehensive view when considering these aspects and their long-term implications.
Applications of PLCs
The realm of Programmable Logic Controllers (PLCs) spans a diverse range of applications, illustrating how integral this technology has become in various industries. PLCs serve as the backbone for automation processes, optimizing production and enhancing operational efficiency. Their adaptability to different environments is a significant factor that has led to their widespread use. This section delves into some of the prominent applications of PLCs, highlighting the value they bring and the specific contexts in which they thrive.
Manufacturing Automation
In manufacturing, PLCs shine as an essential component that drives efficiency and accuracy. They facilitate automation in assembly lines, controlling machinery and processes with precision. For instance, in an automotive assembly plant, PLCs are used to synchronize robotic arms that assemble vehicles, ensuring that each part is placed correctly and at the right time. The primary advantages include:
- Increased Productivity: PLCs can run continuously without the need for breaks, unlike human workers. This leads to higher output levels.
- Consistency in Quality: By eliminating human error, PLCs maintain a consistent quality in products, which is vital in industries where tolerances are critical.
- Real-Time Monitoring: They provide live feedback about the production process, allowing for immediate adjustments to optimize performance.
As industries continuously adapt and evolve, the role of PLCs in manufacturing is becoming more crucial, proving them to be an invaluable asset.
Process Control Systems
In industries like chemical processing and food production, PLCs manage complex process control systems. They monitor variables like temperature, pressure, and flow rates, ensuring that processes remain within desired parameters. For example, in a water treatment plant, a PLC can control the pumps and valves, adjusting to changing water quality or demand. Key elements of PLCs in this context include:
- Automation of Control Loops: They help maintain stable conditions essential for the production of safe and high-quality products.
- Safety Management: PLCs can trigger alarms and safety measures in case of anomalies, reducing risks associated with hazardous materials or processes.
- Data Logging and Analysis: By collecting data, PLCs allow for better decision-making and process optimization, essential for cost reduction and efficiency.
The demand for reliable and efficient control systems continues to grow, solidifying the place of PLCs in this industry.
Building Management Systems
Another area where PLCs prove their worth is in building management systems. These systems automate various building operations, enhancing comfort and energy efficiency. For instance, a PLC can control lighting, HVAC systems, and security alarms. With the rise of smart buildings, their role has never been more critical. Considerable benefits of using PLCs in this field are:
- Energy Efficiency: PLCs enable smart scheduling of energy usage, which can significantly lower operational costs.
- Integrated Control: They allow for centralized management of all building operations, providing a seamless experience for users.
- Scalable Solutions: Whether for a small office or a large commercial complex, PLCs can be tailored to fit the specific needs of any building.
In essence, the integration of PLC technology in building management has led to smarter, more efficient buildings.
Transportation Systems
The transportation sector, with its complexity and need for reliability, has also embraced PLC technology. From traffic light control systems to railway signaling, PLCs are vital for maintaining safe and efficient operations. They can manage multiple inputs from sensors and other devices. Some highlights of their use in transportation include:
- Coordination of Traffic Flow: PLCs can optimize traffic signals based on real-time data, reducing congestion and enhancing transportation efficiency.
- Safety and Monitoring: They enhance safety by managing signals and alerts in transit systems, ensuring that trains and buses operate under safe conditions.
- Adaptive Systems: PLCs can be adjusted to accommodate new traffic patterns or transportation needs, providing flexibility in managing urban traffic.
The future of transportation, especially with the advent of smart city initiatives, heavily relies on the capabilities offered by PLC technologies.
In summary, the applications of PLCs span multiple sectors, reinforcing their importance in automating processes that improve efficiency, safety, and overall operational effectiveness. Investors and professionals should recognize the significance of this technology as industries continue to evolve and seek streamlined solutions.
Advantages of Using PLCs
The landscape of industrial automation is intertwined deeply with the use of Programmable Logic Controllers (PLCs). In the heart of smart factories and advanced manufacturing systems, PLCs play a pivotal role by streamlining processes and enhancing operational efficiency. This section delves into the key advantages that make PLCs essential in todayโs industrial environment.
Flexibility and Scalability
PLCs stand out due to their flexibility and scalability, which are crucial in adapting to dynamic manufacturing demands. A PLC can be programmed and reprogrammed with relative ease, allowing businesses to adjust their operations without the need for overhauling their whole setup. For instance, a manufacturer producing different kinds of products can switch the PLC programming in a flash to cater to varying production lines. This adaptability is not just a convenience; itโs a competitive edge.
Moreover, as a company expands or shifts its focus, scalability allows it to add new modules or controllers to the existing system. Itโs akin to building a Lego setโif you want to create something bigger, you just add more pieces rather than starting from scratch. This kind of growth capability means that investments in PLC technology are not only useful in the present but are also aligned with future expansion strategies, making it a wise choice for any investor.
Reliability and Robustness
At the core of any automation strategy is the need for uninterrupted operation. PLCs excel in reliability and robustness, crucial traits in environments that can be harsh. Much like a sturdy bridge, a good PLC can withstand fluctuations in temperature, humidity, and electrical interferences, factors that often derail sensitive electronic devices. When a PLC is deployed correctly, it ensures minimal downtime, which is essentially the lifeblood of production.
A prime example of this reliability can be seen in the automotive industry, where PLCs monitor assembly lines, ensuring that machinery operates flawlessly around the clock. Unplanned outages can cost millions, not just in downtime but also in lost customer trust. Thus, the dependable operation of PLCs becomes more than a technical metric; it turns into a key performance indicator that investors closely watch.
Ease of Programming and Maintenance
Finally, one cannot overlook the ease of programming and maintenance that PLCs offer. Unlike traditional control systems, which may require specialized knowledge, PLCs employ user-friendly programming languages, such as Ladder Logic. This simplicity offers a gentle learning curve, making it easier for operators to get up to speed and manage the systems effectively.
This approach means that significant time and money can be saved when it comes to training personnel, as fewer hours are needed for onboarding. Additionally, regular maintenance can often be performed by in-house staff, rather than relying on external specialists.
"The flexibility, reliability, and maintainability of PLCs contribute significantly to their enduring popularity within various industries."
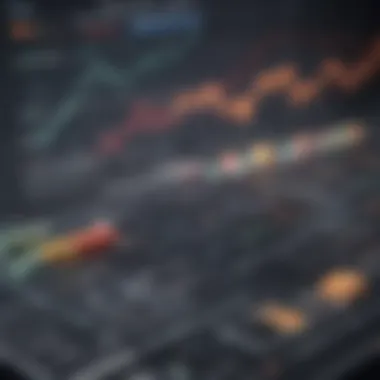
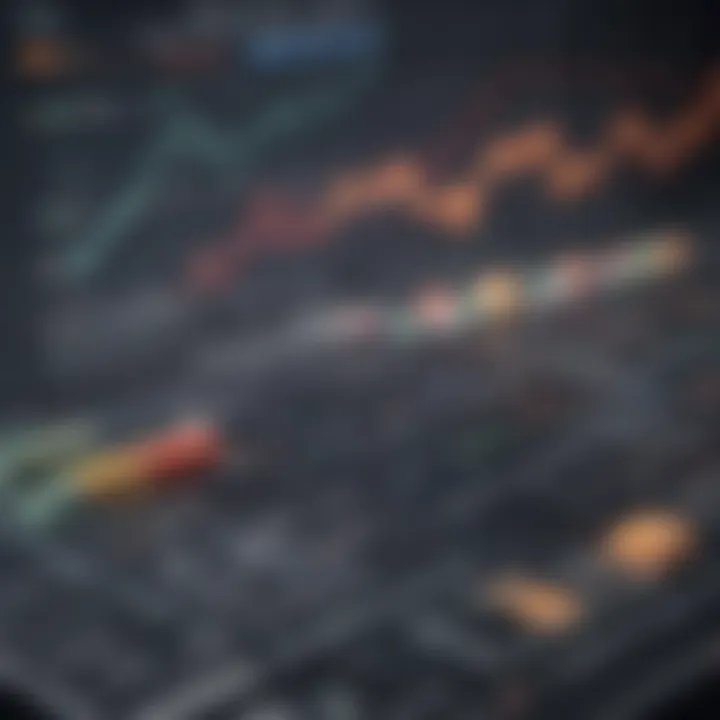
Challenges and Limitations of PLCs
While Programmable Logic Controllers (PLCs) have revolutionized automation, theyโre not without their hurdles. Understanding these limitations is crucial for investors, financial advisors, and professionals who are mapping out the future of industrial technology. The challenges associated with PLCs can significantly influence operational effectiveness, cost management, and long-term planning. Below are some key aspects.
Initial Cost Investment
Investing in PLC technology comes with a hefty price tag. The initial setup involves not just the purchase of the PLC hardware but also related components, such as input/output modules and other peripherals. This upfront cost can be a hard pill to swallow, especially for smaller operations or firms just starting to integrate automation. Itโs not unusual for spends to escalate when including the bespoke requirements for programming software and installation services.
Moreover, ongoing maintenance and troubleshooting can pile on additional costs. Companies often underestimate these ongoing expenditures, which can add up over time, potentially eclipsing the actual hardware costs.
Complexity in Large Systems
As operations scale up, the complexity of managing multiple PLCs increases substantially. Interconnecting various PLC units can be a tangled web, often requiring specialized knowledge to troubleshoot issues. This networked system relies on communication protocols that may not always integrate smoothly, creating vulnerabilities in operations.
For instance, consider a manufacturing facility with dozens of PLCs coordinating assembly lines, quality control, and packaging. If one unit malfunctions or fails to communicate correctly with others, it can disrupt the entire workflow. Even seasoned engineers might find it challenging to diagnose problems in expansive setups, which may lead to costly downtimes.
Dependence on Skilled Personnel
Another significant hurdle is the reliance on trained personnel to operate and maintain PLC systems. Unlike simpler automation solutions, PLCs require specific know-how, making them less accessible to a workforce that isn't specially trained. These skilled professionals often come at a premium, and their expertise can be in high demand across various sectors, leading to talent shortages.
The challenge is further compounded when key personnel leave the organization. Organizations must invest in training, which not only takes time but also resources, to replace skilled employees. The dependency on a niche skill set makes planning for future workforce changes a tricky endeavor.
"The evolution of PLC technology highlights both exciting advancements and ongoing challenges, reminding us that innovation brings new complexities."
In summary, while PLCs offer impressive capabilities for automation, stakeholders must navigate through their challenges, keeping a close eye on costs, system complexity, and the need for skilled labor. Tackling these issues head-on is essential for maximizing the potential return on investment and gearing up for the demands of the future.
Future of PLC Technology
As the evolution of technology continues to unfold, Programmable Logic Controllers (PLCs) stand at the crossroads of numerous advancements reshaping industries worldwide. For investors and professionals looking to stay ahead in the game, understanding the future of PLC technology is not merely a nice-to-haveโit's critical. The agility of PLC systems, combined with advancements in associated technologies, is set to redefine automation as we know it.
Integration with IoT and Industry 4.
The rise of the Internet of Things (IoT) is revolutionizing how we approach automation and control systems, and PLCs are no exception. By integrating IoT capabilities, PLCs can communicate seamlessly with other devices and systems, gathering data in real-time, which can enhance operational efficiency.
- Real-Time Data Processing: Imagine having the ability to monitor machinery in real-time from remote locations. An IoT-enabled PLC allows for instant adjustments, reducing downtime and improving overall production efficiency.
- Predictive Maintenance: By analyzing data patterns, PLCs can forecast potential failures before they happen. This capability minimizes costly repairs and extends machinery life.
- Interconnectivity: As Industry 4.0 emerges, the collaboration between machines becomes paramount. PLCs, when networked with IoT, become nodes in a larger system that shares information across platforms, driving enhanced decision-making processes.
"In the world of automation, the ability to share and act upon information is the lifeblood of tomorrow's industries."
Advancements in Artificial Intelligence
Many might wonder, how does Artificial Intelligence (AI) fit into the PLC picture? The answer lies in its transformative potential to enhance decision-making and operational capabilities.
- Smart Programming: AI can analyze massive datasets to assist in programming PLCs. This leads to more efficient algorithms and quicker response times to changing conditions.
- Autonomous Operations: AI-powered PLCs can autonomously adjust system parameters based on input from various sensors. This non-static capability creates a more dynamic approach to industrial automation.
- Enhanced Learning: Machine learning algorithms can continuously learn from past data, allowing PLCs to adapt and optimize without human intervention. With the support of sophisticated algorithms, these systems become self-learning entities, capable of adapting to new circumstances.
End
In summary, the future of PLC technology holds exciting prospects, driven largely by their integration with IoT and advancements in AI. For investors, understanding these trends is invaluable for making informed decisions. As the landscape changes, those who adapt will not only thrive but also redefine industrial standards.
Investing in PLC Technologies
As automation continues to captivate industries around the globe, the significance of investing in PLC technologies cannot be overstated. The landscape of production and operational processes is evolving rapidly, and PLCs stand at the forefront of this transformation. They serve as the backbone of automation by enhancing efficiency, reliability, and control across various sectors. Understanding the investment dynamics in this arena is crucial for investors and professionals alike who are aiming to dive deeper into this tech-driven revolution.
Market Trends Analysis
Analyzing the market trends surrounding PLC technologies reveals nuanced insights into their growing relevance. Recent years have seen a marked uptick in demand for automation solutions, leading to substantial investments. According to industry reports, the global PLC market is expected to surpass USD 12 billion by 2027. This growth can be attributed to several factors:
- Adoption of IoT: The integration of Internet of Things technologies with PLC systems has expanded their capability, driving investments in systems that can seamlessly connect and communicate.
- Increased Government Initiatives: Various governments are pushing for smart manufacturing initiatives, resulting in favorable policies that encourage investment in automation technologies.
- Growing Need for Energy Efficiency: As companies aim to reduce operational costs and minimize waste, PLC technologies aid in optimizing energy consumption.
"Investing in PLCs today isn't just about technology; it's about harnessing efficiency and driving innovation for the future of manufacturing."
Key Players in the PLC Market
Identifying the key players in the PLC market helps in understanding which organizations are influencing trends and shaping the future. Companies like Siemens, Rockwell Automation, Schneider Electric, and Mitsubishi Electric are leading the charge. Their contributions include:
- Innovative Solutions: These companies continuously develop advanced features, pushing the envelope of what's possible in automation.
- Robust Supply Chains: By maintaining strong logistics, these players ensure quick deployment and support services to clients, enhancing customer satisfaction.
- Global Reach: With operations worldwide, they cater to diverse industries, from automotive to pharmaceuticals, making them pivotal in the PLC market's evolution.
Investors should keep an eye on these key players as their strategies often set the tone for market shifts and evolutions.
Investment Evaluation Strategies
When it comes to evaluating investment opportunities in PLC technologies, a few strategies can provide clarity and direction. Here are some recommended approaches:
- Market Research: Conduct thorough market research to identify emerging trends and technologies that could impact PLC development and deployment.
- Risk Assessment: Analyze potential risks associated with your investmentsโconsider factors such as technological obsolescence or new regulatory frameworks that could alter the marketplace.
- Financial Health of Companies: Review the financial statements and growth strategies of potential companies to determine their stability and innovation potential. A robust balance sheet often indicates a company that's ready for the future.
- Networking: Engage with professionals in the field. Utilize platforms such as Reddit for insights into the current market trends and discussions about PLC advancements, fostering a well-rounded investment strategy.
In summary, the investment landscape for PLC technologies is rich and complex. By grasping market trends, recognizing key players, and employing thorough evaluation strategies, investors stand to benefit from this continually evolving domain.
Epilogue and Key Takeaways
Understanding the complex world of Programmable Logic Controllers (PLCs) is not just beneficial for engineers and technicians; it extends widely into the realms of finance and investment. Professionals in these sectors can glean substantial insights into how automation technologies like PLCs are shaping industries globally. This article has illuminated the multifaceted nature of PLCs, their essential components, and their overarching applications. To encapsulate the value the discussion has brought, letโs delve into the crux of the matter.
Summary of Key Points
- Core Functionality: PLCs serve as the backbone of many industrial automation processes, controlling machinery and streamlining operations with precision.
- Diverse Applications: Whether in manufacturing, building management, or transportation, PLCs are pivotal in ensuring operational efficiency and safety.
- Technological Evolution: From their humble beginnings to integrating IoT and AI, PLCs have undergone significant transformations, adapting to meet contemporary demands.
- Investment Landscape: Recognizing major players and market trends is crucial for any investor looking to capitalize on the rising wave of automation.
This gentle reiteration brings the reader back to the essentials and underscores the importance of PLC technology in current and future economic contexts.
Future Considerations for Investors
Looking ahead, investors should be mindful of several key factors that could significantly affect the dynamics of PLC markets:
- Integration with IoT Technologies: The collaboration between PLCs and Internet of Things devices holds tremendous promise. This synergy can potentially lead to smarter, more efficient operational frameworks across various sectors.
- Advancements in Artificial Intelligence: As AI continues to evolve, its incorporation within PLCs could revolutionize how they operate, enabling predictive maintenance and enhanced decision-making capabilities, thus elevating ROI.
- Educational and Training Investments: With a limited pool of skilled professionals adept in PLC technologies, there is a pressing need for investment in training programs that develop expertise in this domain.
"As industries embrace automation, the significance of PLCs cannot be overlooked. Investors must stay informed to navigate this transformative landscape responsibly."
By focusing on these pivotal aspects, investors can prepare themselves for a robust future in the automation industry, examining not only the immediate returns but also the long-term viability of investing in technologies that are gradually redefining industriar dynamics.